When I was approached by Ian about an office in his garden he was asking about a “posh shed” – the home/office things you see in glossy magazines; just crane them in and off you go. But Ian wanted one that was somewhere around Passivhaus levels of performance and built using sustainable methods. My initial response of “there must be loads out there” quickly faded when I started looking at them all in detail – all were incredibly vague about building fabric performance and bandied around “green” and “sustainable” with the same factually-unsupported abandon as the local supermarket’s usual questionably-sourced products.
My next tactic was to point Ian at Transcore – a construction company in Malton, one of who’s joiners had been in business doing “posh sheds” when I’d last worked with them. However, he’d since left – but Transcore were still up for looking at the project if they could be given a design to price/build. So – I decided it was time to sharpen my pencils.
The brief was basically “a nice room to work in” and the site was the bottom of Ian’s garden, already containing a pondful of nature, requiring clambering over a pile of bikes to get to, and with views of the PV’s on the house roof. I designed a simple one-room building with natural larch cladding; since it would be seen from the house (and to make the inside more fun) I gave it a barrel-vaulted, sedum-covered roof.
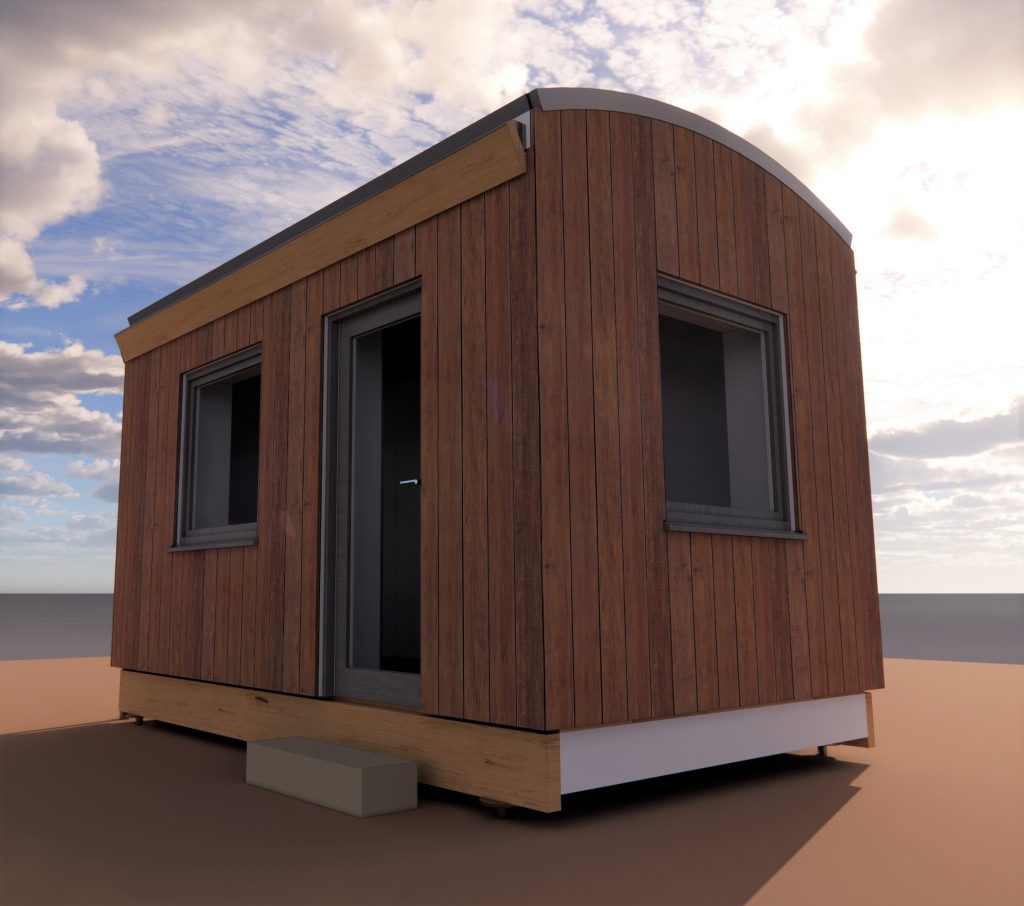
But what to stand it on? There were trees close by that I didn’t want to harm, and with increasing awareness of carbon content of concrete, and the impact that massive foundations have on the overall carbon footprint of buildings, it seemed like time to try something different. I’d heard about steel screw piles being used at Dalby Forest visitor centre some years back but had never seen ‘em in the flesh. Well, this seemed like the time, and structural engineer Robert Thew was happy to work out the loadings and recommend a couple of brands.
Given its height and proximity to the plot boundary the wee building required planning permission (but not Building Regulations approval, unless Ian planned on sleeping in it. I’m assuming a quick afternoon nap is okay…) so drawings and statement (and fee) were submitted and eight weeks later, to the day, planning consent duly plopped into my inbox. Transcore had kept a slot in their workflow for it, and orders were quickly placed for the longer-lead time items – door, windows, and screw piles. A couple of weeks later I got a call from Simon – “due on site in half an hour if you want to watch them go in”, Did I? Of course I did.
Given the access issues, we were relieved to see it was a very small-scale operation; two blokes and a selection of Loony Tunes out-of-scale ironmongery; a hand-drill about six feet long and the screw piles themselves, looking *just” like something from the drawers in Pextons, but held about four inches in front of your face…
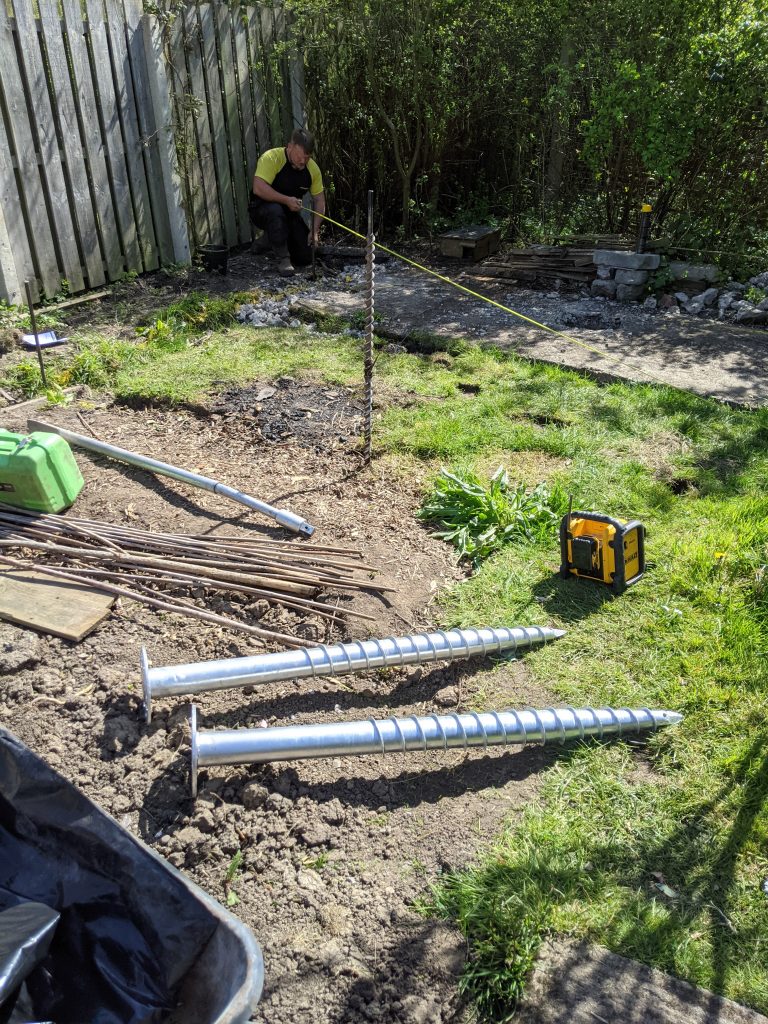
The installers – from Selby company Stopdigging! – reckoned this was the closest job they’d done to home, and that they’re often screwing things into Kent or Surrey, so my business sense tells me this is a market which isn’t yet at capacity. The process was wonderful – pilot holes with the Loony Tunes drill, then just hand-tighten the screws into them…
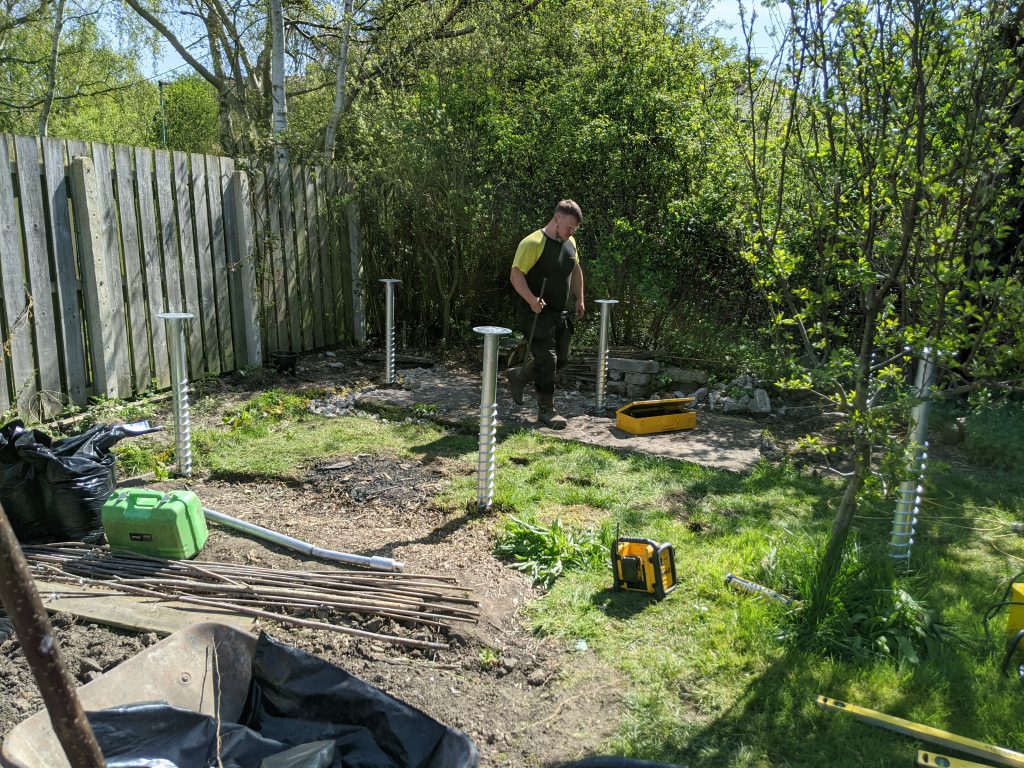
…then each one was wound into the ground using an oversized and under-geared electric screwdriver, with a hinged brace to take the torque and a simple clamp-on sprit level to maintain the upright stance. Once the first was set about 150mm above ground, the rest were monitored on the way in using a laser level – a loud bleep indicating the right moment to stop. No trees were harmed, and the undisturbed grass next to the screws looks really quite surreal, like they’ve been there years.
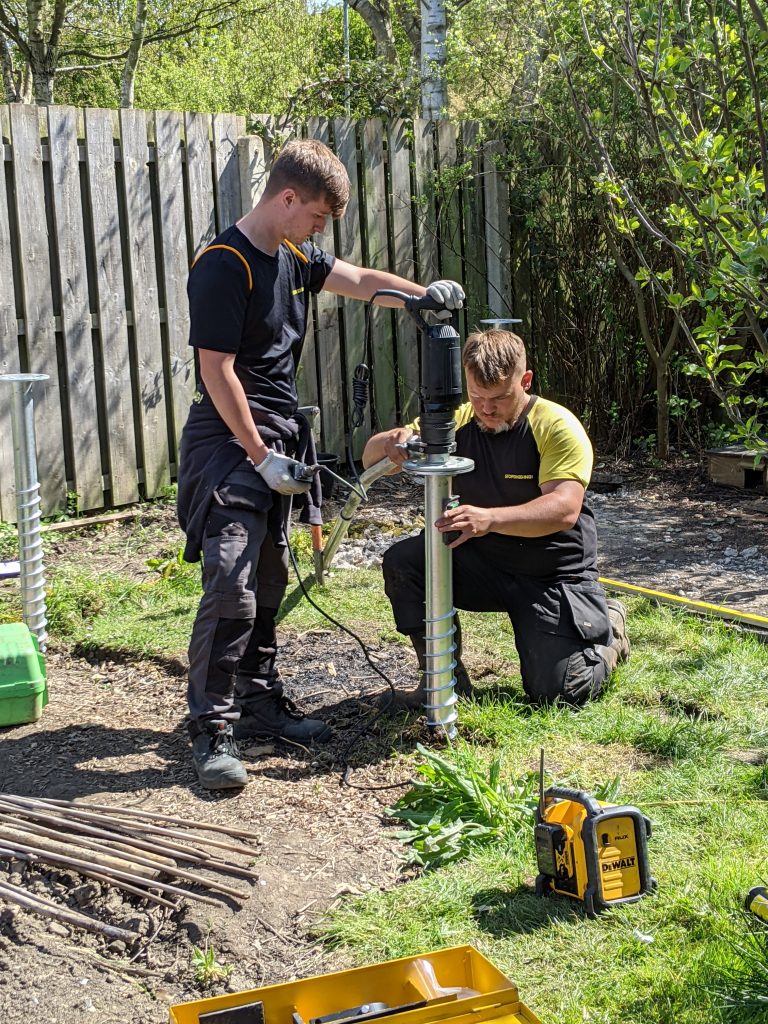
Next step is to put glulam timber beams atop them, and then construct the floor, off which the wall panels will be built and stood upright, and tied together by the roof. It’s not a big job, but it’s fun, and hopefully Ian will enjoy his new work setting.
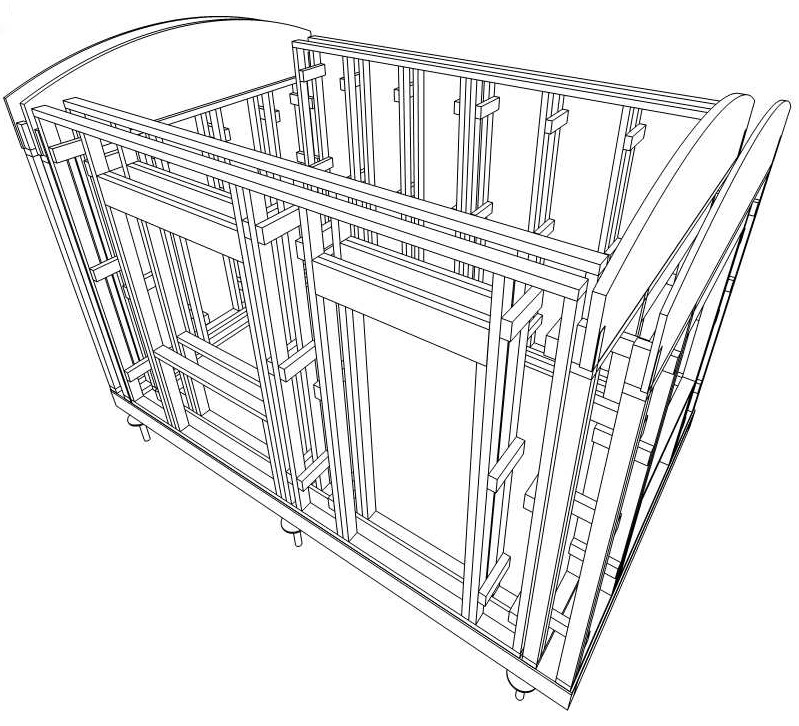
There’s a broader, bigger significance to the project and its screw piles though. At the seriously-sustainable end of construction – Passivhaus territory and likewise – we are starting to respond to the fact that as operational carbon (ie carbon from lifetime use of a building) is reduced by energy efficiency and decarbonising the energy source, then the embodied carbon – the carbon *built into* the fabric of the structure (from raw materials, processing and manufacture, and transport) becomes increasingly significant. We can fairly quickly address the above-ground bits of that – by using more timber, strawbale, and other renewable materials but “stuff in (and on) the ground” is more problematic. How do we reduce carbon inherent in using concrete as a foundation material?
Products like screw piles still bring challenges. The steel still has some serious energy/carbon input, as does the galvanizing to rust-protect them. They give a floor structure above the ground – so a “suspended” floor which means either concrete or timber (but a suspended timber ground floor won’t currently get NHBC approval). But they do at least push discussion – Twitter has been awash with radical substructures talk following photos being posted, and there is gradually developing knowledge out there which is being readily shared. Want to be involved in those discussions?
AECB – https://www.aecb.net/
Zero-Carbon Yorkshire – http://www.zerocarbonyorkshire.org/
Passivhaus Trust – https://www.passivhaustrust.org.uk/